Edition: November / 20182018 Chili Cookoff!
AP&P Celebrates Fall With a Chili Cookoff!
What's Happening
Fall is officially here! Along with cooler temperatures and pumpkin spice lattes, the start of the fall season also means that it's time for our annual chili cookoff!
This year, AP&P decided to hold the cookoff on Wednesday, October 31st.
There was some stiff competition, with three contestants all bringing delicious entries into the contest.
At the end of the luncheon, each team member voted for their favorite chili. In the end, Lu Stroebel was deemed the 2018 Chili Cookoff champion!
Congratulations, Lu!
Preventing Shipment Damage
Tips & How-To's
Although it is impossible to prevent every mishap in your supply chain, you can take action to reduce product damage and returns. David Faulkenberry, Senior Vice President of XPO Last Mile, offers these damage prevention tactics.
- Allow time for testing. Before rolling out a new packaging line, make sure to test its performance ahead of time. Send several shipments that closely mirror the weight, volume, and nature of the products you'll be shipping.
- Use shipping indicators. Attach these inexpensive devices to the outside of your boxes to indicate if a shipment has been jolted, dropped, tilted, or exposed to high humidity. This will allow you to identify and resolve damage trends.
- Seal the deal and cushion the blow. Seal packages with high-quality, pressure-sensitive tape to ensure they are secured closed and protected from moisture, odor, and the elements. Place adequate cushioning between products and shipping containers to protect goods during shipment.
- Fill the void. Empty space isn't just a problem inside boxes. Every significant gap around the perimeter of your packages allows them to shift, fall and collide with other items during transit. To minimize this risk, try to thoroughly cube container and trailer loads, and use dunnage such as airbags to fill in any remaining spaces.
- Factor in the boomerang effect. To ensure protection for returned items, make original packages easy to open and reuse so customers tear, slice, or otherwise compromise the protective materials when opening the shipment.
- Opt for air-ride transportation over spring-ride for high-value goods. Repetitive roadway vibration can mean disaster for your product. Although trucks with air-ride suspension systems can't eliminate the risk of vibration-related abrasions, scuff, or leaks, they substantially reduce the possibility.
- Don't cut corners on box-cutter training and package-opening instructions. Educate your receiving and delivery workers on safely wielding box cutters to avoid scratches, rips, and other costly product damage - as well as injury. Make sure that all boxes display opening instructions - including where to cut and where not to cut - to protect merchandise inside.
- Just subtract water. Container rain or cargo sweat is excessive condensation that builds up within containers due to temperature and humidity shifts. This can cause corrosion, warping, or mold that can ruin your products. To maintain optimal dryness, add desiccants to moisture-sensitive shipments traveling through a range of climatic conditions.
- Give forklifts their due (diligence). Ensure that all areas in your warehouse have clear, uncluttered aisles so forklifts can maneuver easily. Emphasize the importance of using only the handling equipment designated for a task - some product loads can be easily broken or toppled if handled by the wrong kind of equipment.
- Inspect all shipments. Make sure that every person in your products' chain of custody thoroughly inspects all shipped items for any signs of damage or changes in count or condition. They should note down not only what area of a box has sustained damage, but also the specific nature of the damage.
Jean Marie Brendemihl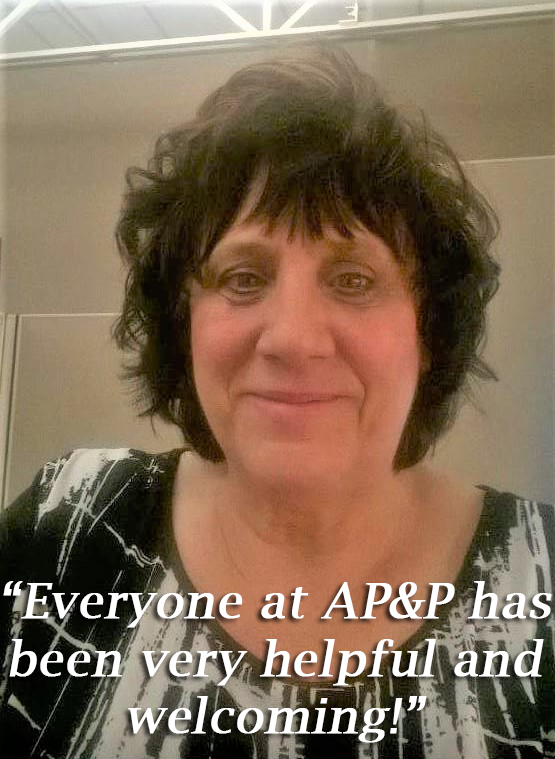
Meet Our Team
Jean is a wife and mother of one son, Nathan, who will be graduating in the spring from West Bend High School. She also is a dog-mom to a Yorkshire Terrior named Buddy. She just started working with us three weeks ago, in Procurement and Customer Service Support.
She has worked in the printing industry for fifteen years, starting as an operator on third shift and working her way up to a position where she managed four departments and was in charge of 100 employees. Jean then went into manufacturing and worked for a plastic injection molding company right down the street from AP&P. In her seventeen years there, she held many positions including customer service, purchasing, scheduling, managing assembly and quality.
Jean has lived in Wisconsin her entire life, and currently resides in West Bend. She is a graduate of Milwaukee Area Technical College (MATC), where she received her Computer Programming and System Analyst degree. She has also received many additional trainings and certifications.
Everywhere that she has worked, Jean has made a point to learn everything she could about how the company operates. This drive to understand and help earned her the "Image Circle Award", an award given to employees that go out of their way to help and contribute to making the workplace more efficient and effective.
In her free time, Jean enjoys golfing and taking family vacations.
Our goal is to raise $10,000 for WHS over the next 4 years. If you want to help kickoff the new program today, we welcome your donations!
Thank you for your generosity!
See Our Progress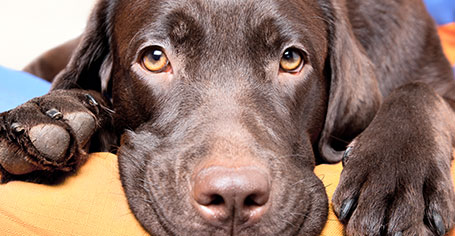
WHS Committment
The Wisconsin Humane Society is committed to providing protection, shelter, and care for wild and homeless animals. Because of generous donors, they are able to rescue, rehabilitate, and rehome thousands of animals like me every year!
Learn More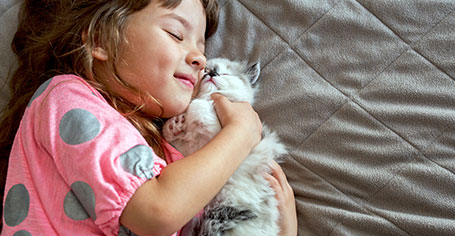
Get the kids involved too!
Got an animal-loving kid? From birthday parties and Kids-Night-Out to awesome summer camps, WI Humane Society has programs for kids of all ages at the Milwaukee, Racine, and Ozaukee Campuses.
Fun Programs